トラブル事例
パーフロ材によく見られるトラブル事例を以下に示しました。
ご使用になられる際の参考にしてください。
また、当社・汎用材のカタログに末尾の『Oリング故障の原因と対策』も参照願います。
ねじれ
主な原因
- 摺動面の仕上げ不良
- ねじれ装着
- 偏心運動している
- 運動が早い
対策
- 摺動面の改善
- 正確な装着
- 偏心の補正
- ねじれにくい材質・形状への変更
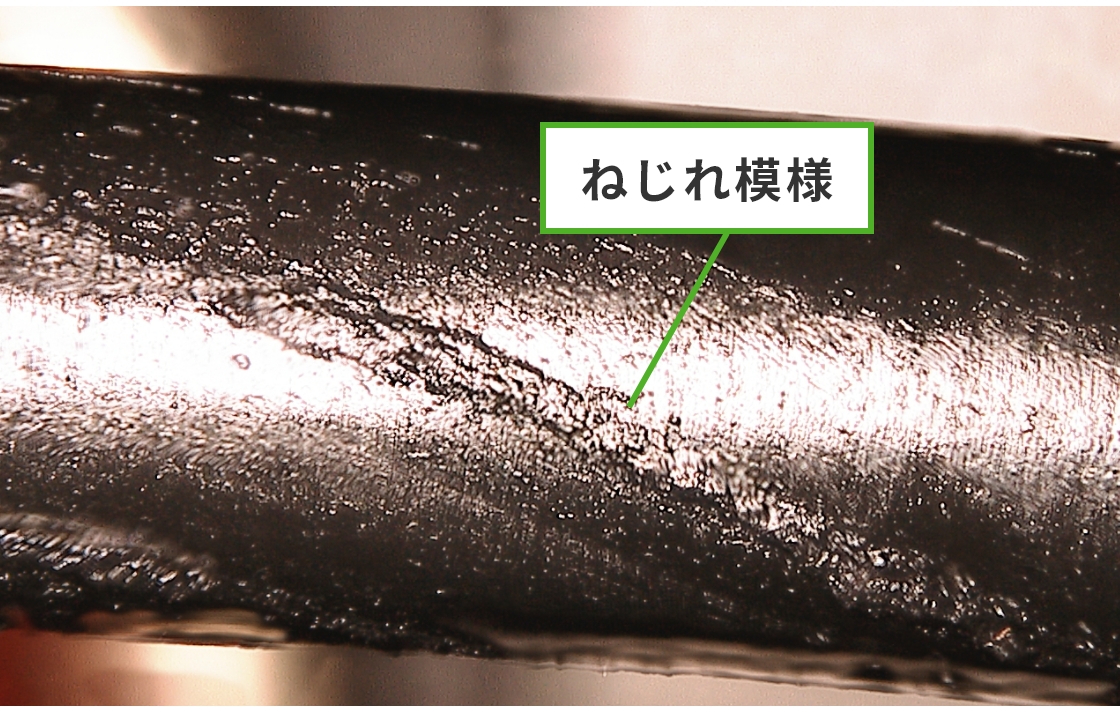
かじり
主な原因
- 正常にミゾに入っていない状態で圧縮し破損
- 正確にミゾに装着する
対策
- 正確にミゾに装着する
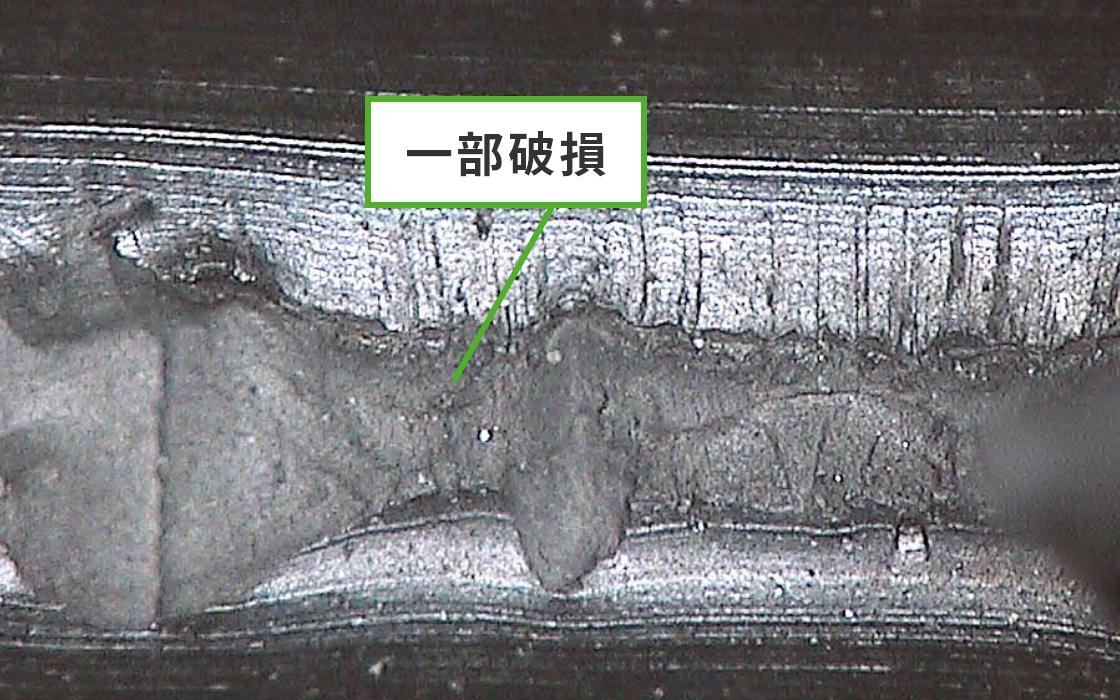
へたり
主な原因
- 耐熱性の問題
- 耐寒性の問題
- 流体による問題
対策
- 材質変更(耐熱性、耐寒性、耐薬品性)
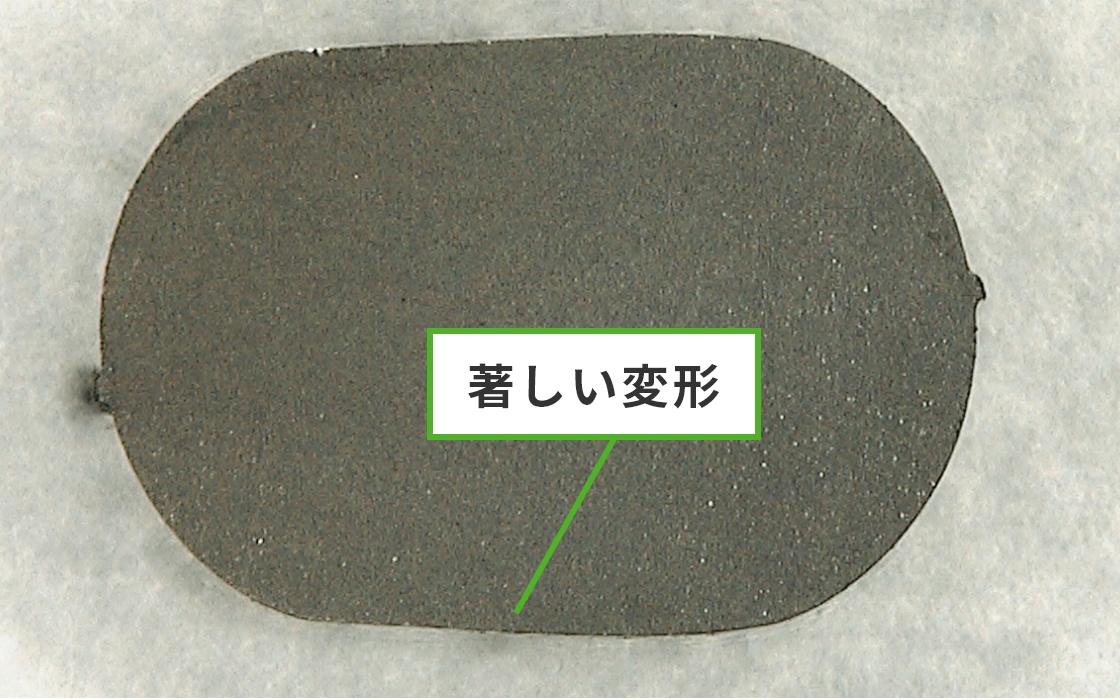
全面摩耗
主な原因
- 摺動面の仕上げ不良
- 潤滑剤不足
- チリ、ゴミなどの異物混入
対策
- 摺動面の改善
- 適切な潤滑
- 異物混入を防ぐ(ブーツなどの追加)
- 材質・硬さ変更(耐摩耗性)
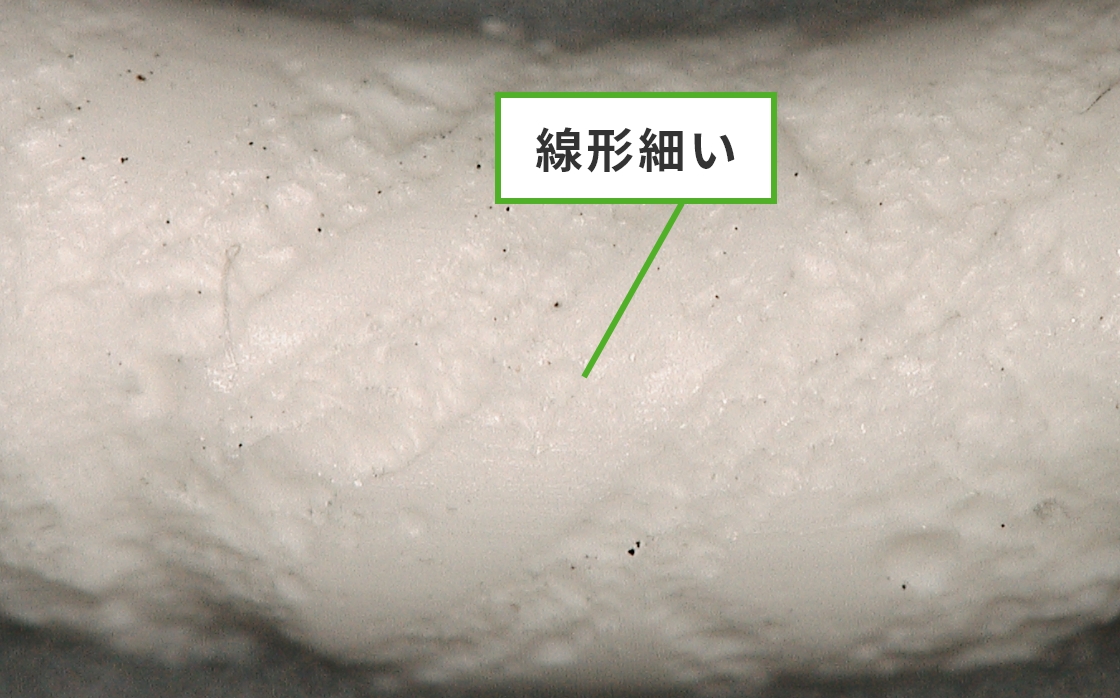
部分摩耗
主な原因
- 摺動面の仕上げ不良
- 摺動面の表面粗さが粗い
- 摺動面にキズ・開口部がある
- 潤滑剤不足
対策
- 摺動面の改善
- 適切な潤滑
- 材質・硬さ変更(耐摩耗性)
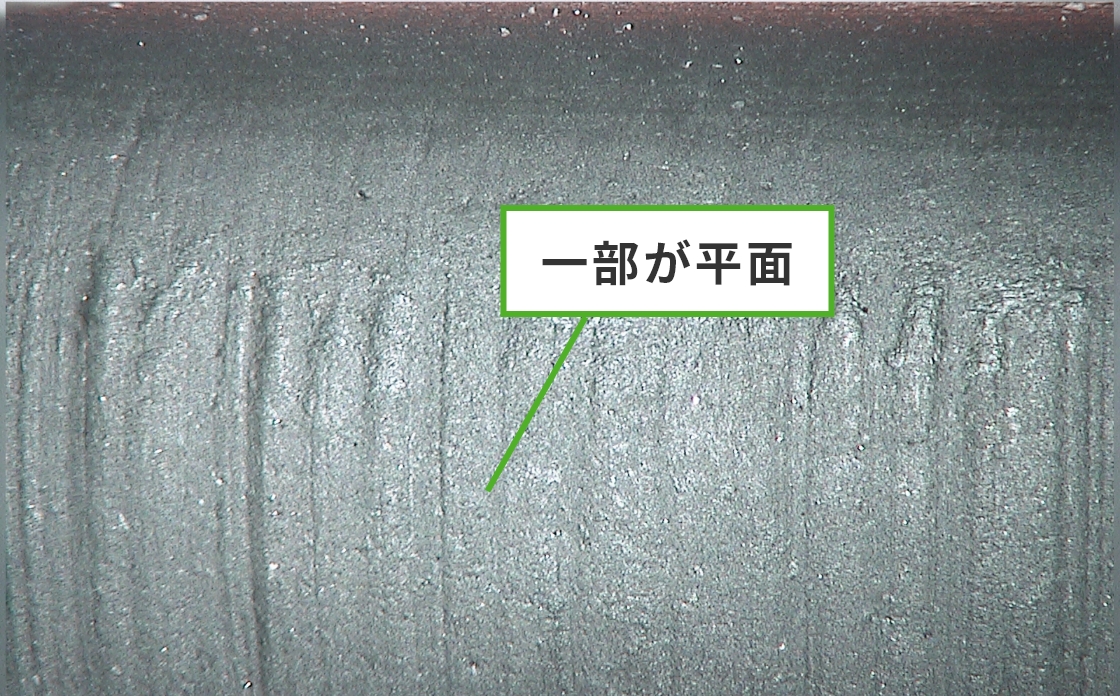
硬化
主な原因
- 耐熱性の問題
- 耐薬品性の問題
対策
- 材質変更(耐熱性、耐薬品性)
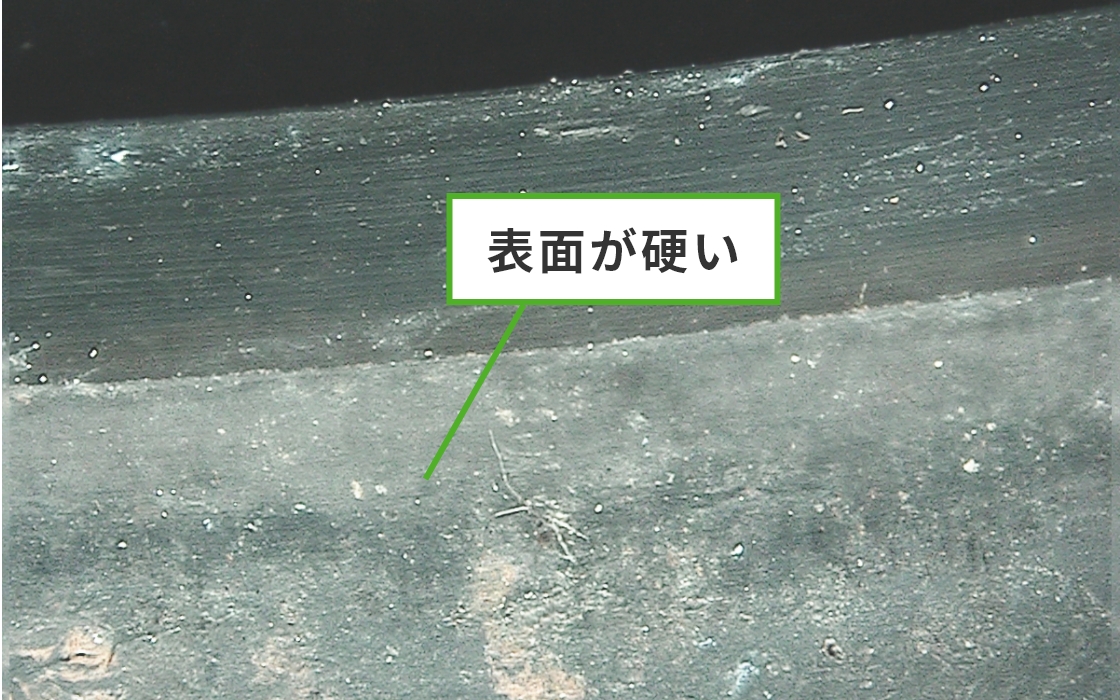
膨潤
主な原因
- 耐薬品性の問題
対策
- 材質変更(耐薬品性)
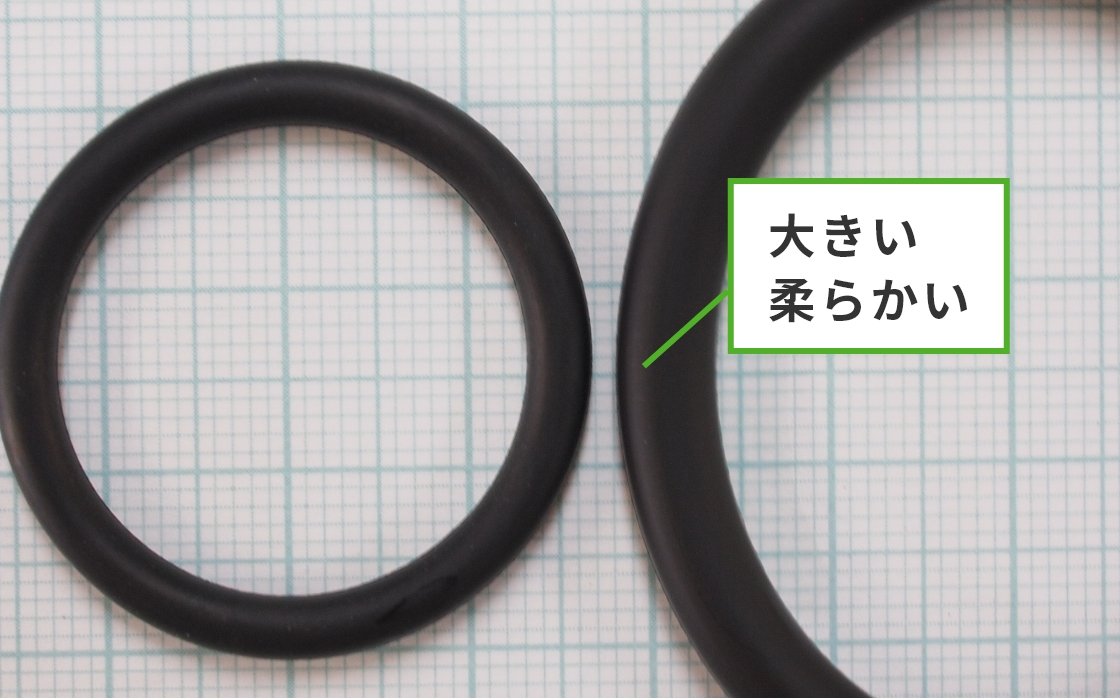
抽出
主な原因
- 耐薬品性の問題
対策
- 材質変更(耐薬品性・低抽出性)
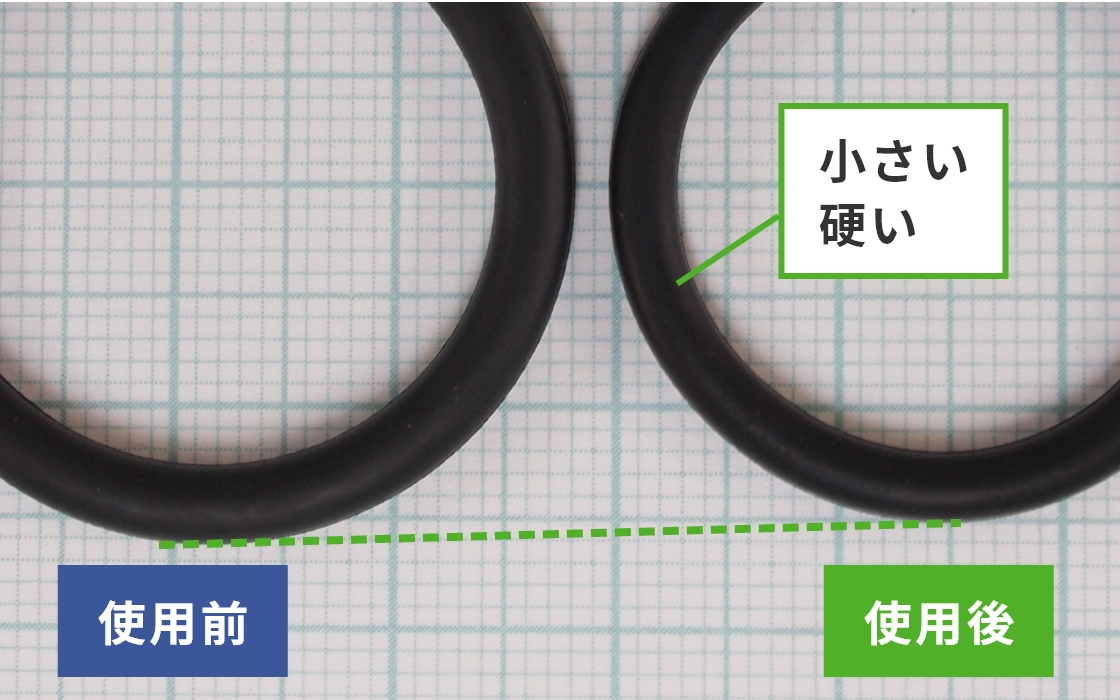
キズ(装着時)
主な原因
- 装着時に相手面でキズをつけた
対策
- 適切な装着
- 治具の使用
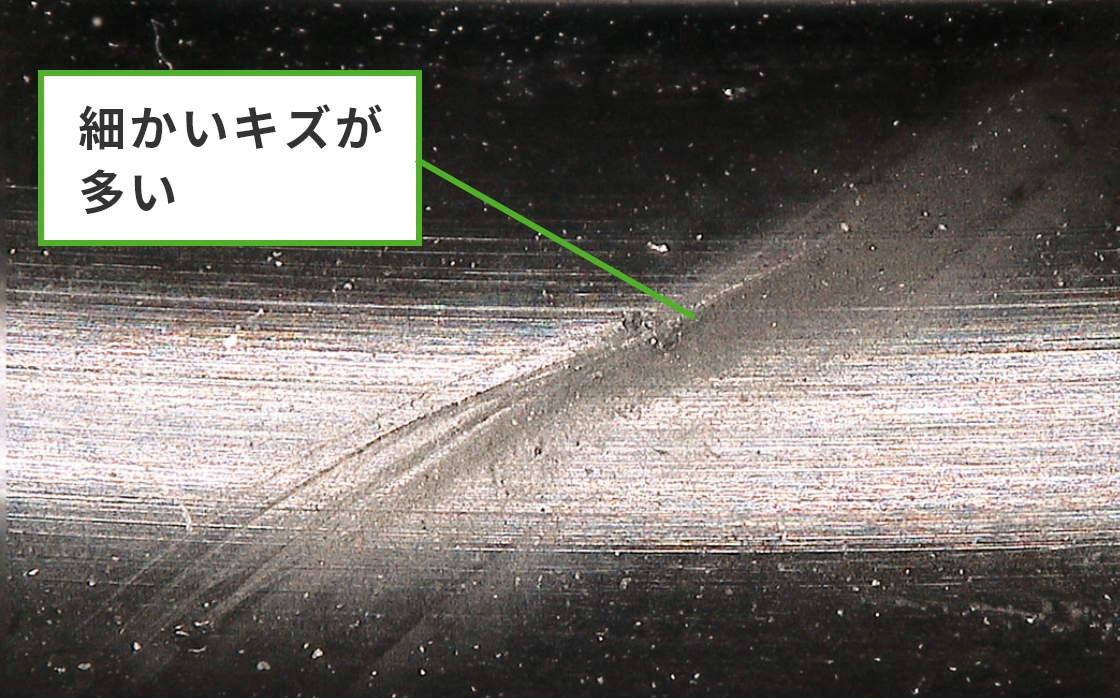
はみ出し
主な原因
- 設計上の問題 (圧力、すき間、硬さ不足)
- 膨潤による
対策
- 設計変更
- すき間を減らす
- 材質、硬さ変更
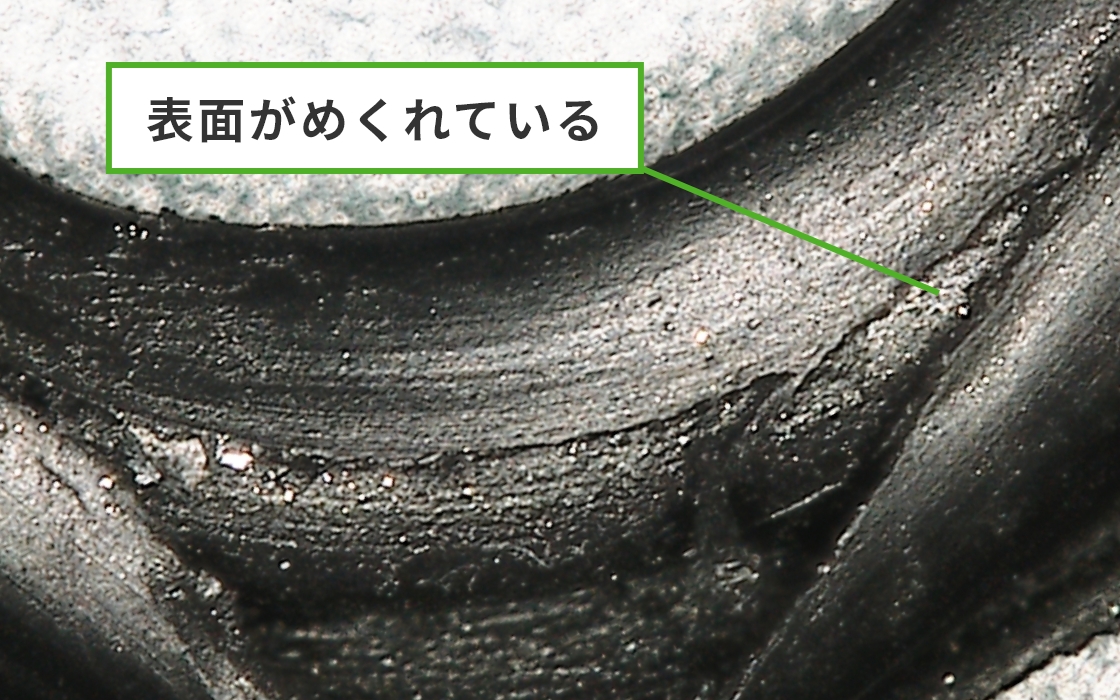
むしれ
主な原因
- ミゾ縁部の面取り不良
- ミゾが浅くて過圧縮による破損
対策
- ミゾ部の面取りを適切に行う
- ミゾの再設計、Oリング寸法の変更
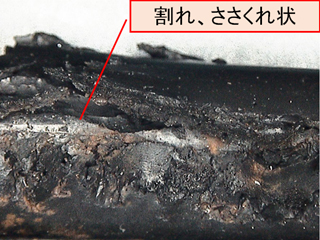
オゾンクラック(NBR等)
主な原因
- 空気中でOリングを伸長させて使用
- 表面にグリス等が塗布されていない
対策
- 材質の変更(耐オゾン性)
- グリースの塗布
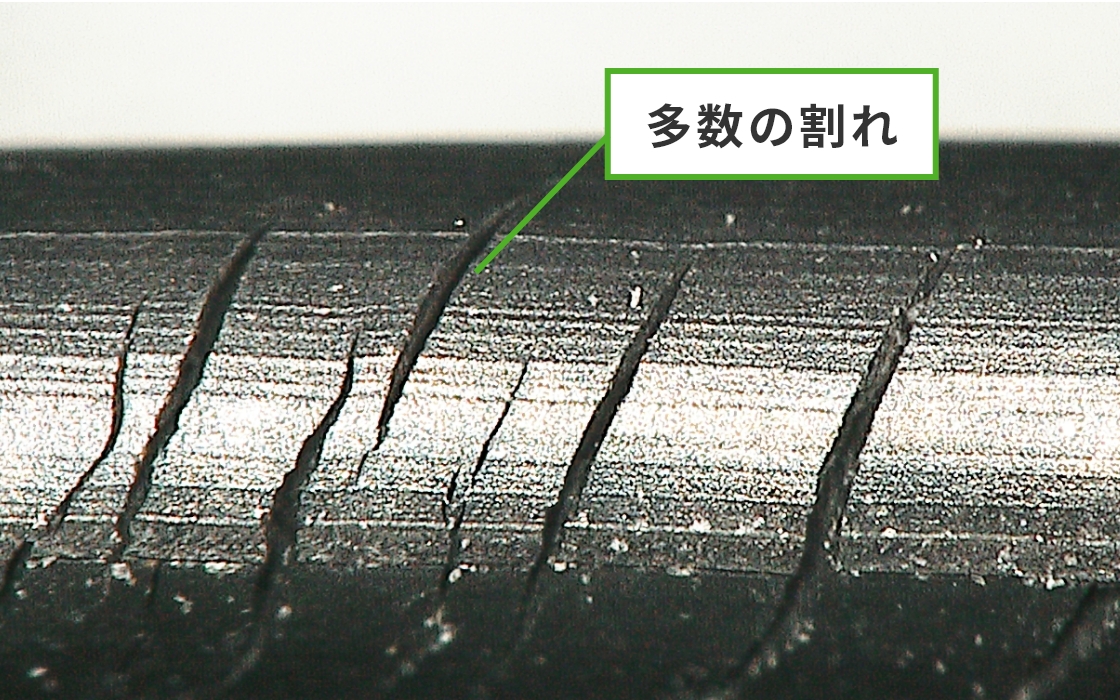
加水分解(耐水・熱水に弱い材質)
主な原因
- 長期間保管した(ウレタンゴム)
- 熱水に接触する環境で使用
対策
- 長期保管しない
- 材質変更(耐水・熱水性)
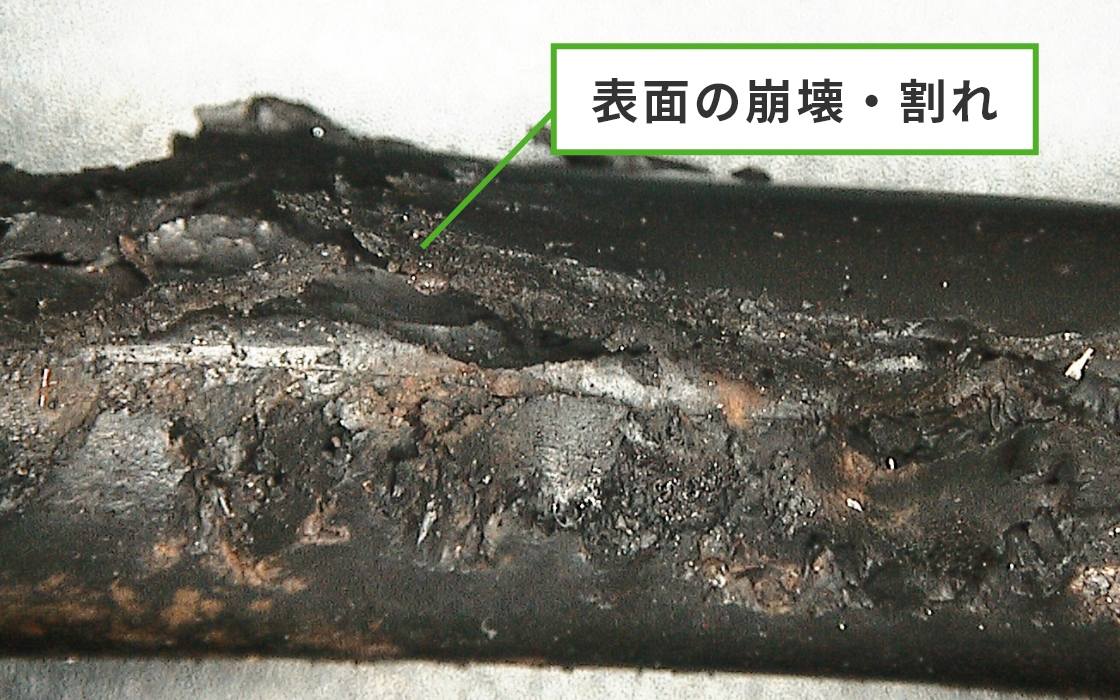
使用流体による劣化
主な原因
- 耐薬品性の問題
対策
- 材質変更(耐薬品性)
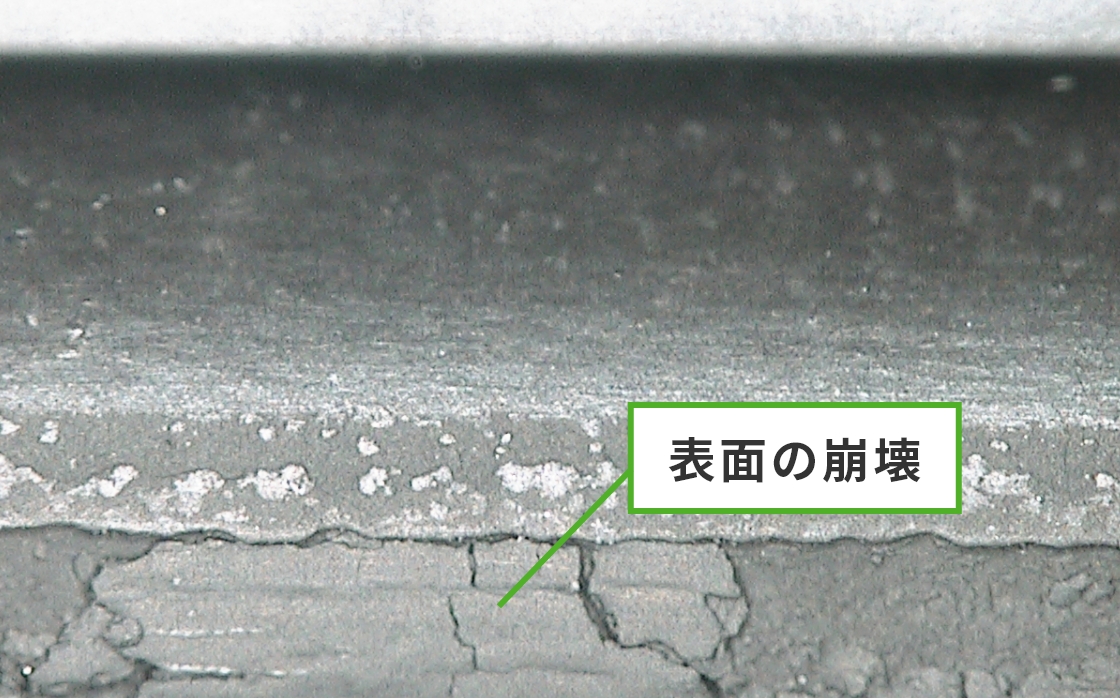
プラズマエッチングによる劣化
主な原因
- 耐プラズマ性の問題
対策
- 材質変更(耐プラズマ性)
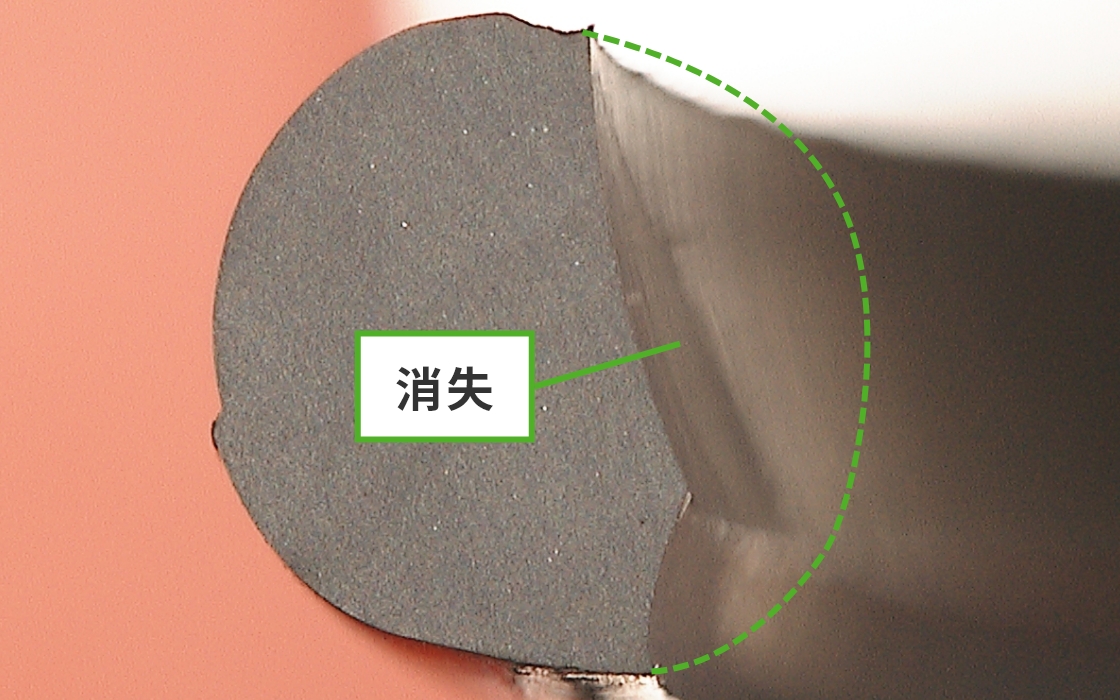
Oリング製品情報 Product
Oリングを選定する際は使用する環境によって材質を、使用するミゾの寸法によってサイズを選定し、
材質とサイズ両方をお選びいただいたものが製品名になります。